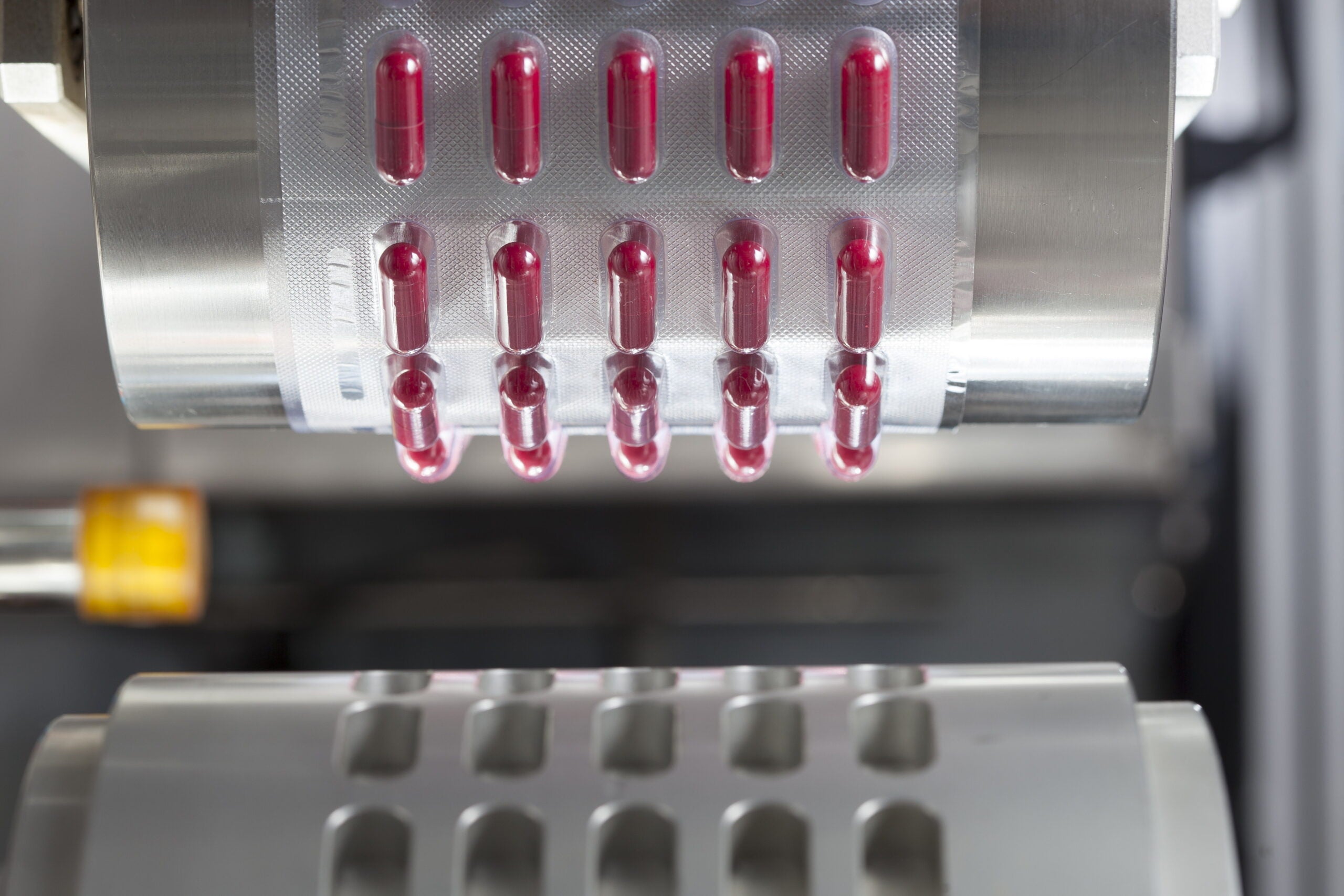
When it comes to getting a drug to market, one of the most complex aspects to manage is the manufacturing supply chain for drugs still in development and undergoing assessment in clinical trials.
Each of the many steps involved in clinical development is plagued with uncertainty, from the patients involved in the trial to the drug itself and how it’s manufactured.
Clinical software-as-a-service outfit N-SIDE has created a suite of services that aims to manage the complexities that go along with clinical trials.
Earlier this month the Belgium-headquartered clinical trial optimisation experts launched a new app to streamline manufacturing planning for the entire clinical program, from drug substance and drug product to the finalised Investigational Medicinal Product (IMP).
By harnessing AI and machine learning, N-SIDE’s new Production App optimises manufacturing for clinical trials, supports evidence-based decision-making and accelerates clinical development timelines. By automatically optimising the usage of production assets and resources, it also helps reduce waste and development costs.
The app has already been piloted by a large pharmaceutical company, resulting in an 11% decrease in manufacturing costs equalling €10.5m in savings, according to N-SIDE.
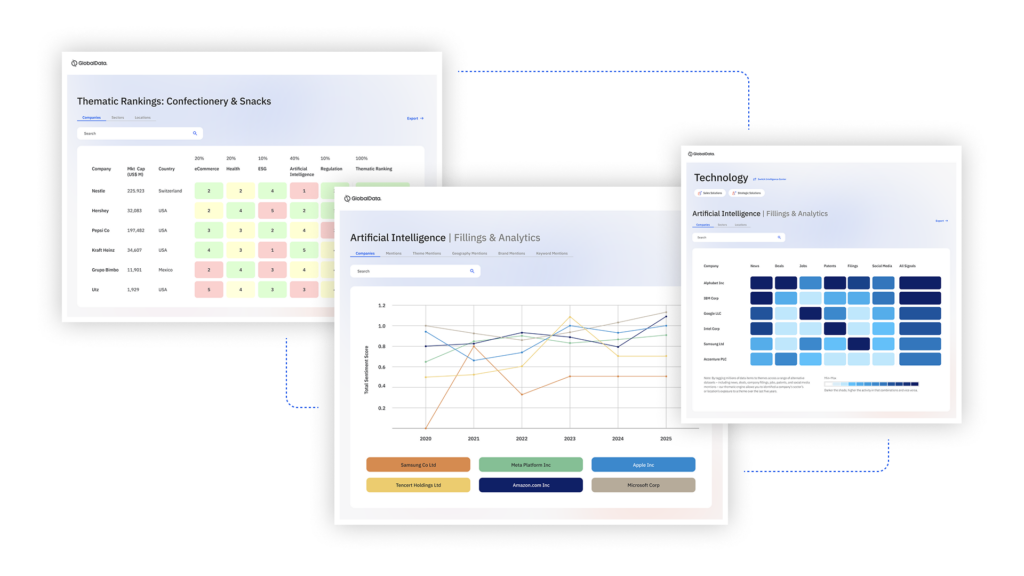
US Tariffs are shifting - will you react or anticipate?
Don’t let policy changes catch you off guard. Stay proactive with real-time data and expert analysis.
By GlobalDataClinical Trials Arena sat down with N-SIDE life sciences director Sébastien Coppe to learn more about the new app and how it is making clinical trial supply chains easier to manage.
Kezia Parkins: How does N-SIDE’s new app optimise manufacturing for clinical trials?
Sébastien Coppe: The main goal of the N-SIDE’s Production App is to optimise the production planning at the clinical program level. Through its seamless integration within the N-SIDE Suite, it provides end-to-end supply chain management. All decisions around manufacturing the drug substance and all the steps to get the IMP to patients are optimised. Moreover, the risk associated with this end-to-end supply chain strategy is proactively assessed.
Clinical development is a dynamic world, full of uncertainty and your supply chain should be ready for almost anything to happen.
With the Production App, we can optimise all the production planning decisions – how much you need to produce in which manufacturing sites, the quantities, the frequency and how to allocate batches to clinical trials. You can also quickly assess different scenarios and see how robust your current supply chain strategy is to changes and various unforeseen events.
With drug development, you also have to manage a lot of aspects relating to the stability of the drug as when biotech/pharma companies start developing them they usually have a really short shelf life.
This is something that was not handled by any other software in the past and that’s where N-SIDE’s Production App is positioned as a unique solution that will not only allow you to handle all the clinical development specificities, the uncertainty in development and clinical trials themselves but also make sure they can be planned in an optimal way.
Using the Production App leads to a reduced budget, reduced waste and reduced timelines. Everything, including manufacturing, is foreseen as a potential bottleneck for clinical development, which means that of course if you can reduce the clinical development timeline then you can reduce time to market.
KP: How important was it for N-SIDE to present this service in an app form?
SC: The main challenge of clinical development is that you never know how the clinical trials will evolve or how the patients will react to the treatment. For example, you may lose a big batch of the drug which could cause a lot of consequences and challenges when you are managing your clinical projects and have to guarantee supply continuity to all patients.
That’s where N-SIDE’s Production App is really empowering CMC [Chemistry, Manufacturing and Controls] and project managers to know whether we can find an alternative production plan without considering this batch – within a single click in the app.

KP: What makes clinical trial supply chains so difficult to manage?
SC: A huge challenge comes from the extreme uncertainty compared to the low average demand per market. It is often difficult to know a few months before a trial starts where we will find patients for clinical trials or how patients will react to the treatment.
Innovative treatments offer huge hope for patients so as a supply chain manager, you cannot take risks with them or have them coming back to a site where they cannot receive the treatment plan. As a supply chain organisation, you commit to perfectly serve this patient demand, whatever will happen.
It’s high uncertainty and a commitment to 100% service levels. That’s really tricky to handle as some drugs will expire. There can be huge timelines for production planning but also for distribution due to regulations, borders and customs. There are a lot of aspects that make supply chains not super reactive to changes but it’s imperative to make sure you don’t have treatments out of stock. That’s exactly the objective of the N-SIDE Production App which allows for management of uncertainty and guarantees that all the patients will get the drug on time. Thanks to the app’s machine learning and optimisation capabilities, it removes the risk and ensures minimum amount of inventories and minimum waste.
KP: With the fast-changing needs of clinical development and trials, what’s the role of the app’s ‘what-if scenario’ planning? Do developers and trial managers have to be proactive about inputting their own plans and expectations to get the most out of this?
SC: Right now, the primary goal within the R&D departments in the industry is to reduce the clinical development timelines rather than reducing budgets. We’ve seen it with Covid-19, where we were able to bring solutions to the world in an amazingly short amount of time.
To achieve this, clinical leaders want to speed up patient recruitment, be able to treat more patients in a shorter amount of time and move faster from one clinical trial phase to another. Many companies want to start planning the next clinical trials without the results of the prior trial as we did for Covid research – planning multiple activities in parallel to reduce timelines.
This can be incredibly complex to manage in terms of manufacturing because it often needs to take place long in advance.
If you want to speed up those timelines you need extra agility and flexibility in the manufacturing process. That’s difficult because there are a lot of production planning activities that are time-consuming and potential bottlenecks.
That’s really where you need to have a robust strategy and the right technology allowing your organization to proactively invest in the right dimensions – for example, have an efficient scale-up strategy in place, invest in process improvement, extra stability milestones, have the right strategic buffers in place without increasing your inventories too much. With such a proactive, data-driven approach, your supply chain will be an enabler for timeline reduction, offering flexibility to even more ambitious clinical plans.
Connecting the dots between all the departments, preventing bottlenecks, allowing [staff] to discuss trade-offs to be made between investments and timelines, that’s really where the Production App is empowering all of those clinical project leaders.
KP: The app was recently trialled by a large (unnamed) pharma company. How did the app help decrease manufacturing costs by €10.5m?
SC: In this case, we were working with a Top 10 pharma company, partnering with their CMC team. On top of standard production planning optimisation, we were trying to understand where there may be aspects that were reducing efficiency and increasing waste. One dimension that we identified was the lot size. This biopharma company used to always manufacture the drug substance within the same kind of lot sizing, systematically producing five litres of drug substance at a time.
We challenged this and advised that they input a range in our Production App between 4 to 5.5 litres. This allows for changes and variation from lot to lot as you often don’t need to supply the same amount over time.
That’s the magic of optimisation. We reduced waste by more than 5% by making sure that manufacturing quantities may be a bit more aligned with the clinical project’s needs along each step.
Another example was about managing the stability plan of their drug candidate to extend its shelf-life. This pharma company’s standard was to assess the extension of shelf life by six months each time. Again we challenged this to advise they reduced the extension by three months at a time instead, to get some extra milestones in between. There was an extra cost as more assessments would be needed and more drug substance would need to be used for that purpose but there would be a benefit as they would be able to supply clinical trials with better shelf life. By challenging this company’s standard we were able to reduce waste again by an additional 5%, which was huge. Sometimes, you need to invest more upstream to benefit downstream.