
In 2019, former head of the US Food and Drug Administration (FDA) Scott Gottlieb stated that the agency had been seeing a surge in cell and gene therapy (CGT) products entering early development.
He emphasised how by 2025, the FDA predicted it would be approving ten to 20 CGT products a year based on an assessment of the current pipeline and the clinical success rates of these products.
At present, 38 CGTs have been approved by the FDA and according to GlobalData’s clinical trials database, there are currently 243 CGT trials underway in Europe.
One key requirement for CGTs is ultra-cold storage, designated as temperatures below -80°C.
In a 2023 report by the American Society of Health-System Pharmacists (ASHP), a drug industry leader noted that the emergence of advanced speciality therapies, like CGTs, would require frozen, ultra-frozen (as low as -80°C) or cryogenic (as low as-196°C) storage.
“This will require planning for additional space, monitoring, storage, and shipping considerations,” the report stated.
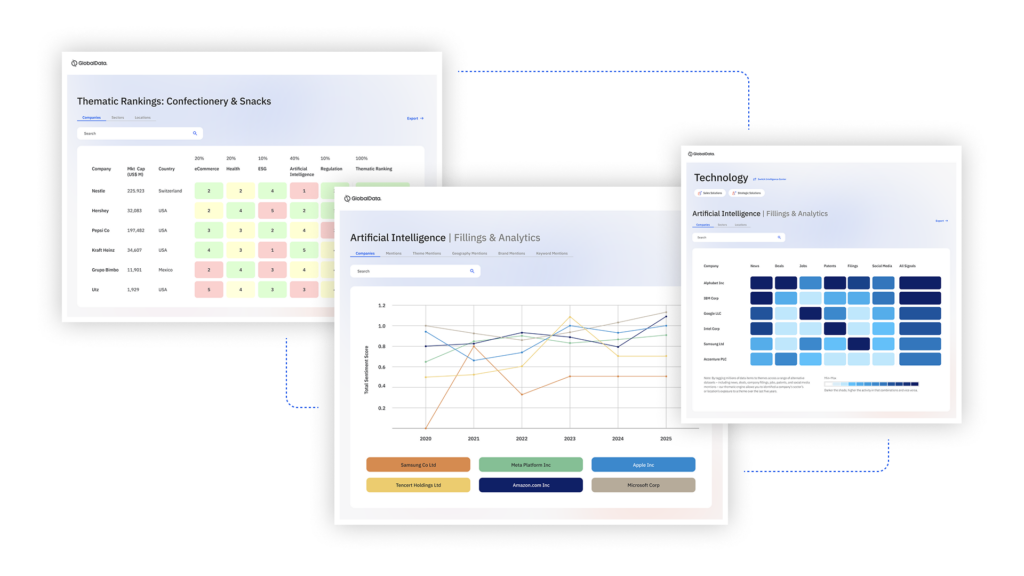
US Tariffs are shifting - will you react or anticipate?
Don’t let policy changes catch you off guard. Stay proactive with real-time data and expert analysis.
By GlobalDataWith a new facility in Bleiswijk, the Netherlands, life science giant Thermo Fisher Scientific is preparing to meet the rising need for cold and ultra-cold storage solutions that only look set to increase for those involved in clinical trials, and as the space for CGTs and other high-value therapeutics, which require ultra-cold storage, continue to grow.
Clinical Trials Arena sat down with Molly Flick, vice-president and general manager, bioservices and speciality logistics at Thermo Fisher, to learn more about the company’s latest facility and how the site is poised to meet evolving customer needs and service requirements.

Cold/ultra-cold storage comes to the Netherlands
The new cold and ultra-cold storage facility in Bleiswijk, Netherlands opened in June 2024.
The company currently has 29 sites globally that serve clinical trials, and the Netherlands facility becomes the 14th site offering ultra-cold storage.
The 5,000m² site provides temperature storage facilities ranging from ambient to ultra-cold cryogenic, the likes of which are required for CGTs and vaccines.
Flick says there also exists the ability to build a mezzanine at the facility, meaning that storage space at the site could effectively be doubled if needs dictate.
“Today, we’ve got capacity for up to 78 liquid nitrogen (LN2) tanks for cryopreservation of cells and microbes, and about 300 -80°C stand-up storage units. We also have walk-in coolers for -20°C, -40°C, and -2°C to 8°C,” says Flick.
“We’re covering all of the temperature ranges, from ambient all the way up to cryogenic, and have ample space in which to do that.”
Advantages of the Netherlands
With a smaller facility in Germany serving intra-Europe for clinical trial needs and one in the UK, the Netherlands was chosen as the base for this larger facility given its geographic benefits.
“The Netherlands is really an international gateway, providing easy access from air, land and sea for European stakeholders,” says Flick.
Flick says the facility is around five times the size of what Thermo Fisher currently has to serve the ultra-cold storage needs of its European customers and notes it has been seeing an increase in drugs that have cold chain requirements, with an accelerated need for ultra-cold storage as growth in clinical trials for CGTs continues.
“We really put thought into our ability to expand our service provision as the market needs of our customers are expanding,” says Flick.
“The sweet spot for the contract development and manufacturing organisation (CDMO) side of the business is really around specialising in all things ultra-cold.
“While we do everything from ambient all the way up to cryogenic, for us, the differentiator is truly around the -80 and greater temperatures that are going into cryogenic.”
The capabilities of the Netherlands facility have been further informed by clients’ clinical and commercial needs.
The facility contains seven suites for kitting and packaging, with the added capability of being able to do multi-language and patient-specific secondary packaging at labelling at the site.
Operational availability has been another key factor in the planning of the Netherlands facility.
“Operational hours are a requirement where nowadays you need to be operating seven days a week,” says Flick.
“We’ve therefore made provision at this site to staff for seven days and 12 hours per day because you never know when those critical requirements for life-saving drugs are going to arise, and that’s really a key thing that we’ve focused on.”
Flick adds that with the Netherlands facility, Thermo Fisher has thought carefully about the Qualified Person (QP) release. This is a process that ensures the safe release of medicinal products (MPs) for clinical trials or commercial distribution.
“We’re staffing with a robust QP model to help supplement what our customers may or may not be doing themselves,” says Flick.
“Oftentimes, your smaller biotechs don’t necessarily have the infrastructure, so they’re looking for more of that partnership in their approach, whereas your larger biopharma typically has a lot of infrastructure and backbone that they can rely on.”
In providing end-to-end support, Flick also views Thermo Fisher’s transportation provision as a key element in supporting clinical trial customers and can offer bespoke services depending on customers’ price points.
“We have solid transportation services that have been around for 25 years and upwards where, depending on customers’ requirements of criticality, we’re able to meet their needs, from a price standpoint as well as making sure that things are there,” says Flick.
“We’ve done things such as charter planes to make sure drugs get there tomorrow,” she adds.
Thermo Fisher also has a transportation consultancy business that is part of its CDMO unit. As a consultant to its transport partners, this provision can offer further guidance in meeting more complex customer transport demands.
In ensuring customer peace of mind, Thermo Fisher has a real-time track and trace program to show where shipments are, agnostic of carrier.
“We have up to 42 global suppliers that we work with today for transportation, and with our real-time trace and track network, clients can follow shipments to find out where they are but also to ensure that they are staying at the required temperature,” says Flick.
“If we notice that something is not holding temp for whatever reason, we’re able to sometimes intervene and make those changes that will help secure that.”
With temperature excursions being an obvious concern when storing high-value therapeutics such as CGTs, the Netherlands facility itself uses Lab Watch, a temperature monitoring system that Thermo Fisher has used for years across its network, on its LN2 tanks and refrigerator and freezer systems.
“We have redundancies on those systems, and we also have redundancies on our generators and our LN2 tanks,” says Flick.
“We’ve learned throughout the years that yes, having a generator is good, but having two is better in case of failure,” she adds.
Thermo Fisher also works closely with local providers to make sure that they have diesel fuel ready to go to supply its generators.
“We work with the local municipality in the Bleiswijk region to ensure that we’ve got the right support model in case there’s ever a need to implement business continuity planning,” says Flick.
“I would say that our business continuity planning is robust and what we’ve learned through experiences in dealing with these things globally has served us well because you never know what may happen and it is best to be prepared.”
Thermo Fisher has the goal of meeting net zero emissions by 2050.
While acknowledging that there is some difficulty in being sustainable when running operations for therapeutics that need to be kept ultra cold, Flick says Thermo Fisher has taken advantage of solar panels at the Netherlands site and that it runs as a gas-free facility.
She adds: “We have approximately 160 solar panels that are installed on the roof of the Bleiswijk facility that provide us with energy energy through that source. As a gas-free facility, we’ve got electric heat pumps that we use throughout for the heating and the cooling of the facility, and we also have a heating system that is under our floor.”
Future outlook
Looking to the future, Flick says it has become clear to Thermo Fisher that it needs to be able to scale to support the commercialisation of drugs that require cold and ultra-cold storage.
“We’re doing things commercially today out of our Germany site, but this site is on a much larger scale and will really be able to support our clients as they grow,” says Flick.
She notes that for a facility such as this one, it is not just about supporting large-scale companies that need Thermo Fisher’s services.
“I think our sweet spot has also been on working with those small biotechs who actually need us to be an extension of their model,” says Flick.
“They may not have a lot of investment that is focused solely on keeping things ultra-cold. They know they need to do it but knowing how to do it successfully from a supply chain standpoint, is really where we come into play and become that valued partner for them.”
“Making sure that we’re continuing on that journey of understanding all of our clients’ needs as they’re going through their clinical trials and being able to support them from a commercial standpoint and in a robust fashion, is highly important to us.”