With the rise of cellular therapies and individualized medicine, cold chain study management has become a common issue in the clinical trial setting. Let’s take a look at some of the issues surrounding trial material at -70C and colder. Ultra-low and cryogenic products are not new areas and there are already many great standards out there for you to use. If your material does not have unique requirements, then there’s no need to reinvent the wheel.
Product Stability
Product stability studies need to account for allowable processing temperatures and possible temperature excursions during all aspects of the clinical supply chain. With low temperature products come the very real chance of temperature excursions. It is recommended that a temperature excursion map be developed that sets the pre-determined limits for temperature excursion events that include both allowed time and temperature limits. Long investigations after a temperature excursion in the midst of a clinical study are typically not possible.
Decisions on acceptability need to be made within a few days, and sometimes within a few hours. Back-up supply should be considered to replace investigational product when temperature excursions of your product stability data cannot support the excursion, or you have not done the studies yet to cover the excursion range. When temperature excursions do occur, be sure to keep a record of these excursions and decisions on product use. Also, accumulated processing times and allowed temperature excursion times may need to be tracked for a given batch.
Product Labeling
Choosing to label prior to initial freeze will greatly reduce the exposure to the product and expense of operation. Labeling post freeze is not something that can be undertaken lightly. On this note, be aware of all regulatory requirements for labels in the countries your study will be conducted, or in countries you might consider adding later during a study.
Ensuring your labeling will stand-up over your storage and use time is also something that needs to be evaluated. Check with your label provider that printed labels are appropriate for these conditions.
Product Packaging
When it’s time to package, it’s all about exposure. If your study requires secondary packaging, reducing exposure becomes an even larger concern. Stability information on acceptable processing temperatures and times is a must. All packing processes will be based on product stability. There are many options for limiting exposure during secondary packaging, from simple processes to large scale equipment. Your packing company should be recommending options based on your product’s needs.
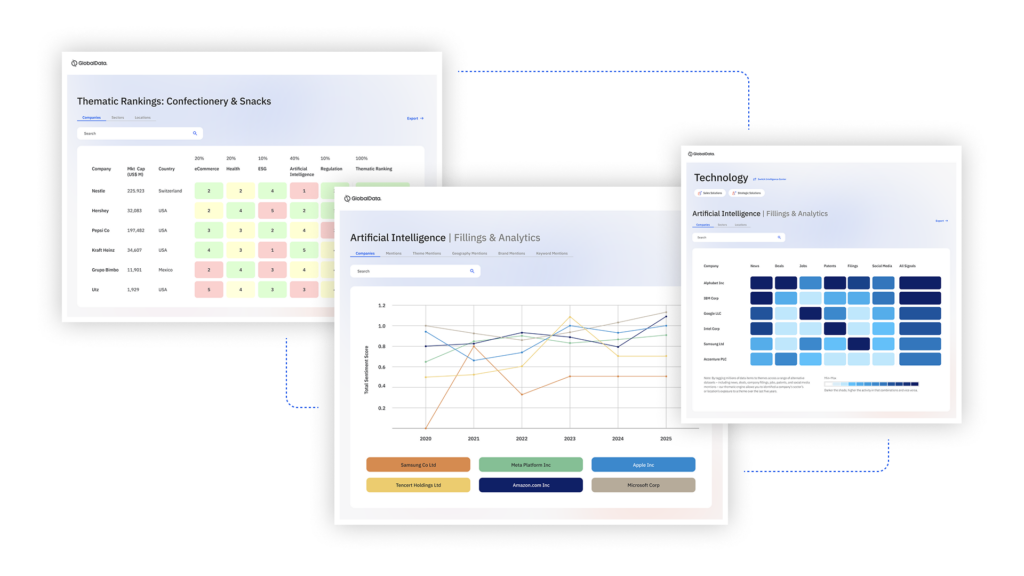
US Tariffs are shifting - will you react or anticipate?
Don’t let policy changes catch you off guard. Stay proactive with real-time data and expert analysis.
By GlobalDataAlways keep the shipping methods in mind when formulating secondary packaging. Consider using a secondary package configuration that is standard in the industry and the transport container you will be using. Many of these configurations have been designed to make efficient use of space in transport containers. The limits of available shipping containers in the -70C and cryogenic realms are much tighter than in other, warmer ranges. Understanding what limits your shipping methods while designing your packaging will save countless headaches and expense throughout the course of your study. Work with your packaging and distribution company to determine preferred methods of shipping while designing your packaging.
Product Distribution
While developing your distribution processes, understanding the limitations of your shipping methods and monitoring devices is important. Acclimation excursions, space constraints, federal regulations, and reliability of electronic monitoring devices should be discussed with your provider. When setting your range of allowable excursions, include verbiage to cover potential electronic failures in monitoring devices.
Understand that no device can guarantee 100 percent functionality at -180C. Some transport providers offer specialty services for handling ultra-cold shipments and a wide variety of costs and range of capabilities is seen in the industry. Choose a company for distribution that has a track record of shipping under ultra-cold conditions and is closely aligned with the transport provider. Additional contingencies on handling return of frozen product need to be considered as well.
Clinical Sites
When selecting study sites, ensure each site has equipment and procedures in place to handle -70C or cryogenic products, as well as on-site transportation methods for dosing as appropriate. Having created acceptable thawing procedures and time limits for preparation and dosing will assist in vetting if a site is suitable. When your pharmaceutics development team are developing these procedures, they should be doing so with the site environment in mind, and not how they would be doing this in a formulation lab.
Summary
Careful considerations should be made well prior to the start of a clinical study with an ultra-low or cryogenic product. Developing stability studies and allowed temperature ranges/excursions ahead of time is critical. There are many companies already working in cold chain and ultra-low cold chain management.
Make sure to check with your trial management company to see what standards they use and have had success with. Where applicable, choosing industry standard primary packaging will allow a much smoother transition as the product moves through the supply chain.
Colin Enz
Validation Manager
CSM
Russell Brierley
Director of Clinical Supply
Lupin Research Inc