There are many challenges that come with setting up and running a clinical trial, not least of which is packaging for transport. While many considerations must be weighed when basing your decisions around transport packaging, the landscape is easily divided into sections that can make or break the design process. Once you have a full understanding of the Study Protocol, the process of designing a transport packaging solution can begin.
A full understanding of the protocol is the best starting point because this document will provide the requirements for the transport services and payload definition(s). This will also make you aware of the complete picture required for the study, for example, a requirement for blood samples from the patient after dosing. Where does the sample need to go? What temperature must the product ship? How quickly does the sample need to travel (i.e. what is the product’s expiry date)? Is this an International study – or is it confined to one country?
How well do you really know your competitors?
Access the most comprehensive Company Profiles on the market, powered by GlobalData. Save hours of research. Gain competitive edge.
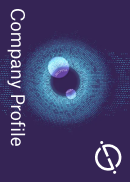
Thank you!
Your download email will arrive shortly
Not ready to buy yet? Download a free sample
We are confident about the unique quality of our Company Profiles. However, we want you to make the most beneficial decision for your business, so we offer a free sample that you can download by submitting the below form
By GlobalDataFor the purposes of this article I have made some assumptions to simplify this example. Changing these assumptions will result in one or more choices in the selection process changing to accommodate the new requirement(s). Let’s consider a trial where the therapeutic product must be shipped overnight by plane at 2-8 degrees centigrade in a domestic (USA) market. I will point out some of the challenges for a few variations as side-bars during the course of this article. Given the above definition we have a lot of information to begin designing a successful solution to our transport packaging challenge. Based on these assumptions, we know we will ship the drug via air to a domestic market at 2-8°C. Now let’s design a solution.
Payload: The materials that you are transporting – this would include the Product, and any ancillary materials that are required by the protocol (how much space do you need within the package?)
Shipping Package: This consists of the outer fibre box, and inner cooler/insulated container, the product will be shipped in.
Cooling System: This is a useful method for maintaining temperature over time within the package. This could be as simple as dry ice, or a complex system of Phase Change Materials that require special pre-conditioning.
Let us start with the Payload – it is best to know what volume (space requirements) is needed for the materials that will be distributed, before adding the cooling system. Once we have accommodated these two parts, we can clearly define the outer package. In this instance we will plan for only a 15mL bottle of product that must be kept frozen with no ancillary materials. To keep the material cool, we can use ‘blue-ice’ – reusable packs that can be pre-conditioned in a freezer. Let’s plan on using three 8 ounce ‘blue Ice’ packs for transportation. We have now solved two of the three items we need to complete this project – the inner cooler must have sufficient space for the blue-ice packs (our cooling system) and the product.
‘Blue-Ice’ and Alternatives: Blue-Ice is a generic term for a saturated salt water based gel in a plastic pouch (or hard plastic container) that can be pre-conditioned in a freezer (-20°C for 24 hours min.) to maintain a certain temperature over time. The term is used to differentiate from ice (frozen water) which, while can be effective in keeping items cool for periods of time, generates a liquid as it thaws that must be contained per shipping regulations. The packaging for ‘blue-ice’ solves the containment issue; they are re-usable and prevent the payload from getting wet. There are many variations of this system. Some use a ‘brick’ or open cell foam that allows the unit to maintain a shape when frozen or thawed. Others are encased in a rigid polypropylene container. An alternative to this are Phase Change Materials that are claimed to hold tighter temperatures for specific time periods. These are usually proprietary materials that need to be pre-conditioned properly and will then perform as claimed. These can be a good choice if the return of the package is guaranteed, as they have a higher initial price.
Now we are ready to consider the Shipping Package. This is a system of inner cooler contained in a fibre, or cardboard outer box. Given that we are using air freight for our transport, this package, and the way we pack the payload, falls under the regulations of IATA (International Air Transport Association). These regulations govern many aspects of packaging and should be consulted prior to finalizing the design. In general, a fibre outer box that contains an inner cooler will be an acceptable solution. We spoke earlier about sizing the interior dimensions of the cooler to accommodate the product (payload) and the cooling system that we choose, as this needs to be done with an eye towards minimizing any excess space. This will prevent the materials from being jostled, and possibly damaging the product, during transport. Additionally these packaged are usually charged based upon a dimensional weight, where the actual weight of the package is less than the ‘average’ package of that cubic size, and so it is charged for the cubic space that the package occupies.
There are two other areas where the IATA regulations come into play for our package solution. Both areas are concerned with the Product being transported. Firstly, if the product is a liquid, it must be in a liquid tight container that is then placed into a secondary container with absorbent material. This is to ensure that in the event the package and the product container are damaged, the liquid will be absorbed and contained. The second area regards the chemical and biological classification of the product with respect to Hazardous or Dangerous Goods classification. This is an important area of compliance, however, this is beyond the scope of the article. You should take care to determine the classification of the product and properly placard the outer fibre box for safe transport. Violations are expensive and can risk being denied as a shipper.
At this point, it’s key to factor in the Cooling System process. The cooler can be made of a number of different materials, and again, cost, performance and durability are the primary factors for making a decision – See side bar on Materials.
Once the components are selected, the total package can be clearly defined:
- A cardboard box to contain the cooler,
- A cooler with sufficient capacity for cooling system and payload.
- The labeling on the outer box must accommodate classification, addressing and shipping instructions with most small package services, the computer generated Air-bill will have the service level encoded into the barcode and label.
Now, with a sufficient inventory of materials, equipment to pre-condition the cooling system (-20 C freezer for blue-ice, see manufacturers for PCM), and a stock of the drug/product to be distributed, all you need next is the list of recipients and the schedule of when to ship.